RING SPINNING YARN DETECTION SYSTEM
Industry background
At present,textile enterprises’ efficiency are mainly affected by labor costs, equipment status, business operations and other factors,spinning process is the key process of quality of spinning mills,difficult to manage,the most direct response to its management is the data of yarn breaks.Therefore, how to detect and reduce breaks is the top priority of spinning management.We know that 30% to 35% breaks are caused by 5% backward spindles.The traditional method is to find out these 5% defective spindles by traveling,repairing by mechanic workers and sampling by testers,but there are many disadvantages.
We developed on-line detection system.It can timely and effectively locate the breaks position of the machine,and greatly improve the working efficiency of the ring frames.Our company aims to provide advanced intelligent modification service for the spinning process of textile enterprises,accelerate the upgrading of the spinning equipment to improve the competitiveness of the enterprises, and spare no effort to help the users to maximize the profit by using the efficient and intelligent means of production control.
System composition
The system is mainly composed of monitoring devices and actuators.
The monitoring device includes single spindle monitoring device.
Tactuators mainly consists of four parts:break photoelectric sensing system,roving stop feeding device,gear end control display and end break warning indication.Schematic diagram of the system modules is shown as picture 1 below. (Among them,spinning management platform intelligent spinning cloud system,energy consumption monitoring,environment monitoring,break and weak twist tower lamp indication,spandex setting,suction fan speed setting,siro setting are optional modules,without optional modules then will not display corresponding data).
System Functions
The monitoring and control system has the functions of single machine indicator and display, gear end display, workshop display, main server display, roving end break stop feeding, timely discovery of breakage and precise positioning, helps to grasp the key points of the quality of the spinning process,reduces labors and waste and improves quality.
Its particularly prominent is that the system has added the production management system for spinning. It can collect data from the mass data, generate various graphic and text reports according to the needs of customers, help the factory technology and management personnel to analyze, manage and make decisions, and provide the convenience of management for the users.
The production management system mainly includes the following functions:
A) Able to display spindles with mote breaks , timely find fault spindle and notify mechanic to repair;
B) No need manual to check break quantities of 1000 spindles/hour and doffing breaks can be viewed online at any time;
C) No need manual copying the yield of production of each shift,the system automatically generated;
D) Can display spindle speed, avoid low speed spindle and reduce weak twist;
E) At any time,can check the varieties of spinning and machine conditions for varieties scheduling;
F) Able to see the operation and running rate of all machines;
G) Can see the relation of speed and other parameters at any time and can optimize speed.
System features
The monitoring and control system of the ring frame is an information and intelligent means.It can record all the data and make the work more open and transparent,thus assisting the management of the workshop group,and providing scientific basis for the enterprise to make decision and optimize process.The system has below obvious features
A) There is no wire connection between each sensor.Direct inserting.
B) The photoelectric (or electric magnetic)probe has the advantages of accuracy and sensitivity,probe is small,the installation distance between the probe and ring is large, and no influence on piecing yarns and the replacement of traveller.
C) The roving stop feeding device is suitable for parallel and V drafting forms.It adopted flexible modules connection,no need extra circuit lines,automatically identify the spindle position, with simple structure and convenient installation and maintenance.Roving stop device sensitivity within 4 seconds.
D) Each set with screen with human-machine interface,provides quick operation instructions for the workers and the mechanic.
E) Design with wifi function,for future remote service,laptop and hand set stable wireless connection.
Meaning of break monitoring module
The breaks detection module of the system is mainly reflected on the lamp and the display. Different display categories represent different meanings.Details as below form 1.
Position |
Categories |
Implication |
Spindle position |
Blue light wink |
breaks |
Red light wink |
fault |
|
Red light on |
Weak twist |
|
Purple light wink |
Sensor being covered |
|
lamp |
Green light on |
1-4 breaks |
Yellow light on |
5-9 breaks |
|
Red light on |
10-24 breaks |
|
Red light wink |
Breaks above 25 |
|
2 colors alternate wink |
Drafting warning/motherboard fault |
|
Display |
Letter b+number |
Break quantity |
Letter E+number |
Weak twist quantity |
|
Letter F+number |
Fault quantity |
Adapted machine main technical parameters
Monitoring system adapted to below form 2 parameters,other parameters customized by requirements.
No. |
Item |
specification |
1 |
Suitable for yarn kind |
14-100s cotton and blending |
2 |
Numbers of spindles |
Short frame、Long frame |
3 |
Type of drafting |
parallel and V drafting |
4 |
Spindle gauge |
68.75MM、70MM、75MM |
5 |
Diameter of shaft cradle |
28MM、40MM |
6 |
Type of ring |
Plane、Conical |
7 |
Spindle number |
From gear end (L/R) in Order |
System technical specification
The system can realize intelligent real-time online monitoring. Its working principle and working diagram are shown in table 2 and table 3 respectively.
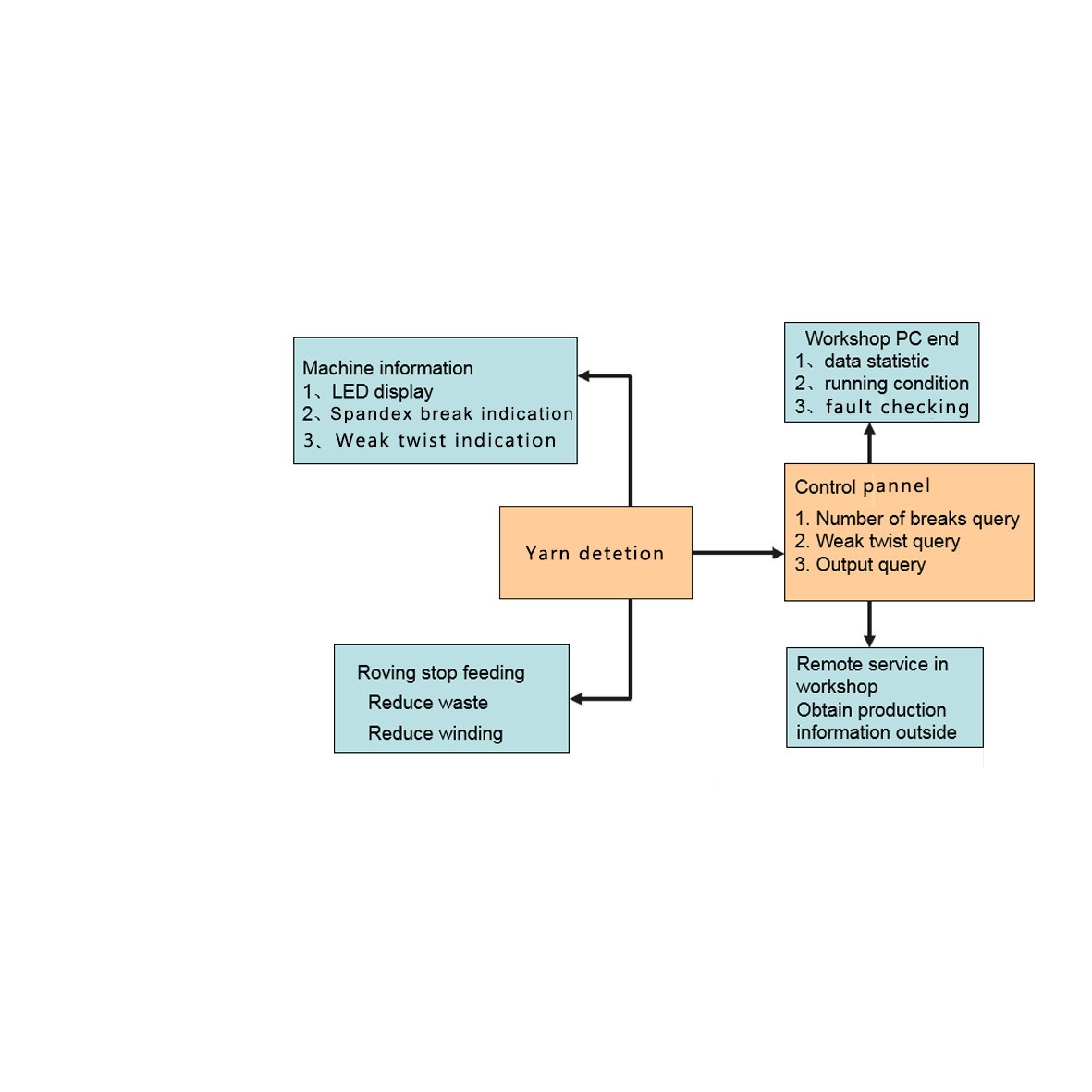
Yarn detection system working principle
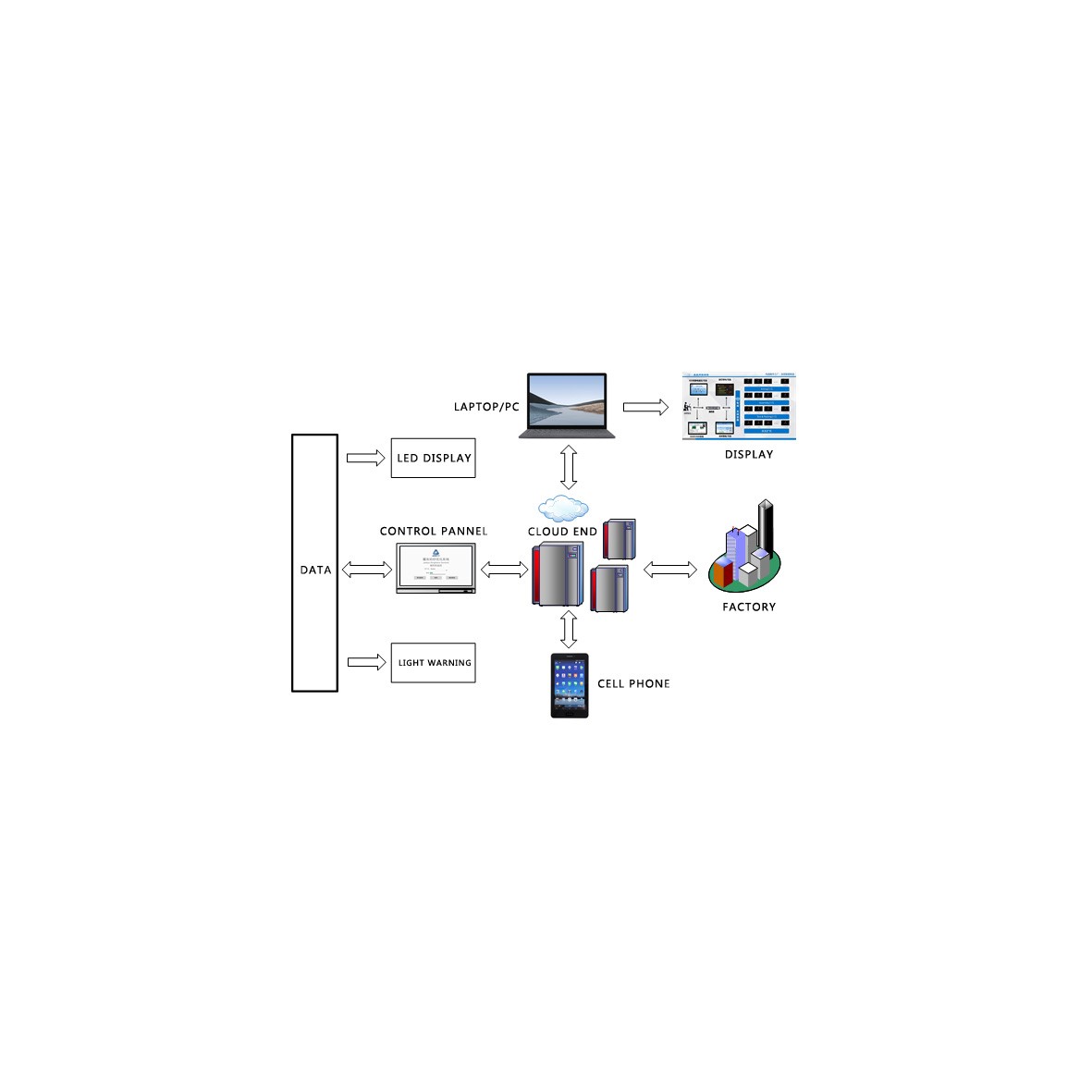
Yarn detection system working diagram
The monitoring system of spinning frame is intelligent, informational and lightweight. Its main technical specifications are shown in Table 2 below.
Item |
Content |
JADEYO single spindle monitoring system 2.0 |
Hardware |
Performance of sensor |
Photoelectric、Magnetic |
Sensor board specification |
24 spindles 0.7kg |
|
User end type |
Support PC,mobile,laptop,wristbands etc. |
|
Roving stop |
At the same time when break happens |
|
Drafting control |
Display roller diameter,current speed |
|
Production monitoring |
Display yarn kind,production rate,length,yield,doffing times etc.. |
|
Breaks happened/1000 spindles/hour |
On line check spindle speed and end breaks happened/1000 spindles/hour |
|
Doffing breaks analysis |
On line check spindle speed and breaks happened/1000/hour of each doffing |
|
Alarm of end breaks |
Sensor light wink,gear end controller shows break position and display shows break quantity |
|
Slight twist |
Sensor light on can on line check spindle speed,break quantity |
|
Way of transmission |
The integrated circuit board easy insertion |
|
software |
Networking with other monitoring devices |
Multi machine networking can form spinning and end break monitoring network. |
Usage of parameter table |
Existing reports can be adjusted according to needs, and later can be customized to develop and set up new reports. |
|
Data sharing |
Data is fully open, data interface supports Ethernet, compatible with HMES manufacturing execution system, ERP resource planning system, OA office system and so on. |
|
Software function upgrades |
Can be developed again and have expansion function |
|
Quality standard |
All spindles on line detecting |
Accurate without misinformation |
Daily failure rate of detecting probe and other electrical components |
Within 1/10000, the service life is more than 10 years |