China Indigo Rope Dyeing Range supplier


Specifications
1 | Machine Speed (Dyeing) | 6 ~ 36 M/min |
2 | Padder pressure | 10 Tons |
3 | Airing Length | 40 M (Typical) |
4 | PLC, Inverter, Monitor / PLC | ALLEN-BRADLEY or SIEMENS |
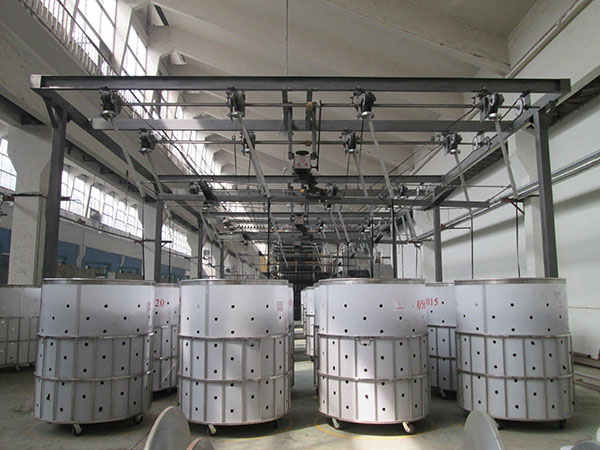
Coiler Cans
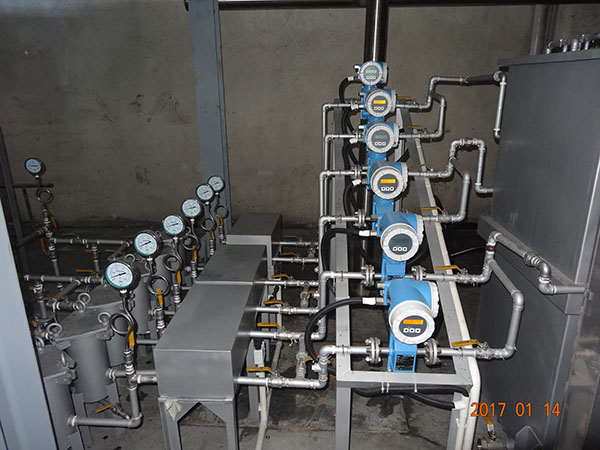
Dosing & Circulation
Features
1 | High Productivity |
2 | High Indigo Pickup |
3 | Best Color Fastness |
4 | Best Shade Evenness |
5 | Best Production Flexibility |
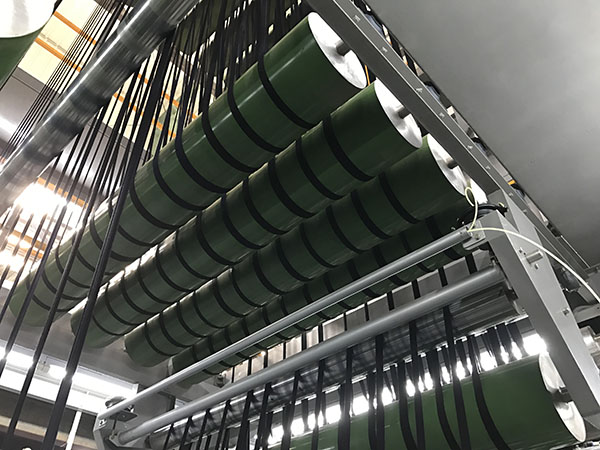
Dry Clinders
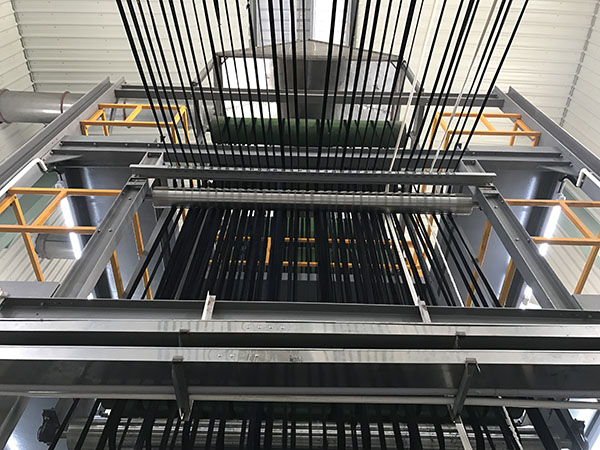
Yarn Exit After Drying
Principles for Indigo Rope Dyeing Range
1. Yarn is first prepared (by ball warping machine for rope dyeing, by direct warping machine for slasher dyeing) and start from the beam creels.
2. Pre-treatment boxes prepare (by cleaning & wetting) the yarn for dyeing.
3. Dye boxes dye the yarn with indigo (or other types of dye, such as sulfur).
4. Indigo is reduced (as opposed to oxidation) and dissolved in the dye bath in the form of leuco-indigo in an alkalic environment, with hydrosulfite being the reduction agent.
5. Leuco-indigo bonds with yarn in the dye bath, and then brought into contact with oxygen on the airing frame, leuco-indigo reacts with oxygen (oxidation) and turns blue.
6. Repeated dipping and airing processes allow indigo to gradually develop into a darker shade.
7. Post-wash boxes remove the excessive chemicals on the yarn, additional chemical agents may also be used at this stage for different purposes.
8. dyed yarn (in the form of ropes) will need to undergo the process of rebeaming (on rebeaming machines, aka LCB / Long Chain Beamer) to break the rope and wind onto warp beams for sizing, before weaving. Or, in case of knitted denim, cone winding is done after rebeaming, to prepare cones for circular knitting.
9. Rope dyeing is generally superior in terms of dyeing result (color fastness, higher indigo pickup, shade evenness, etc.).
10. Rope dyeing can also be used for knitting yarn, while slasher dyeing cannot (without major modification).
11. Rope dyeing requires bigger initial investment, and also requires extra machines (LCB, sizing) and space.
12. Production capacity: About 60000 meters yarn by a 24 rope dyeing range, about 90000 meters yarn by a 36 rope dyeing machine
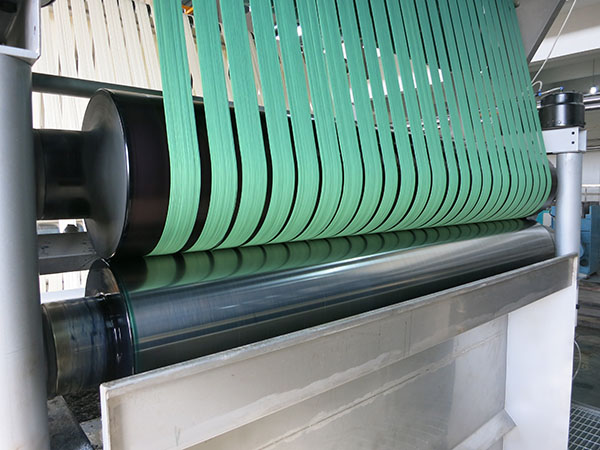
Padder
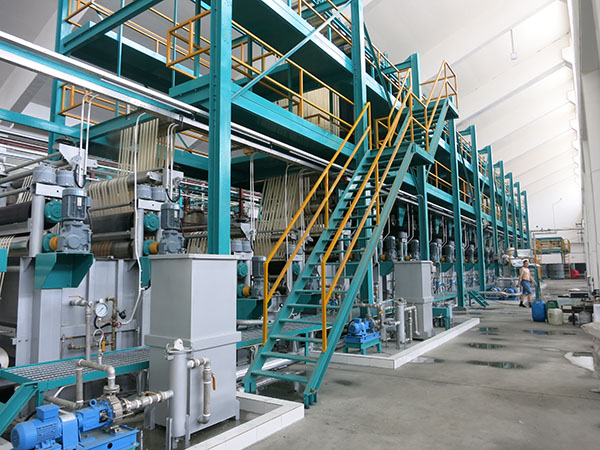
Framework & Ladder
Video
Dyeing process